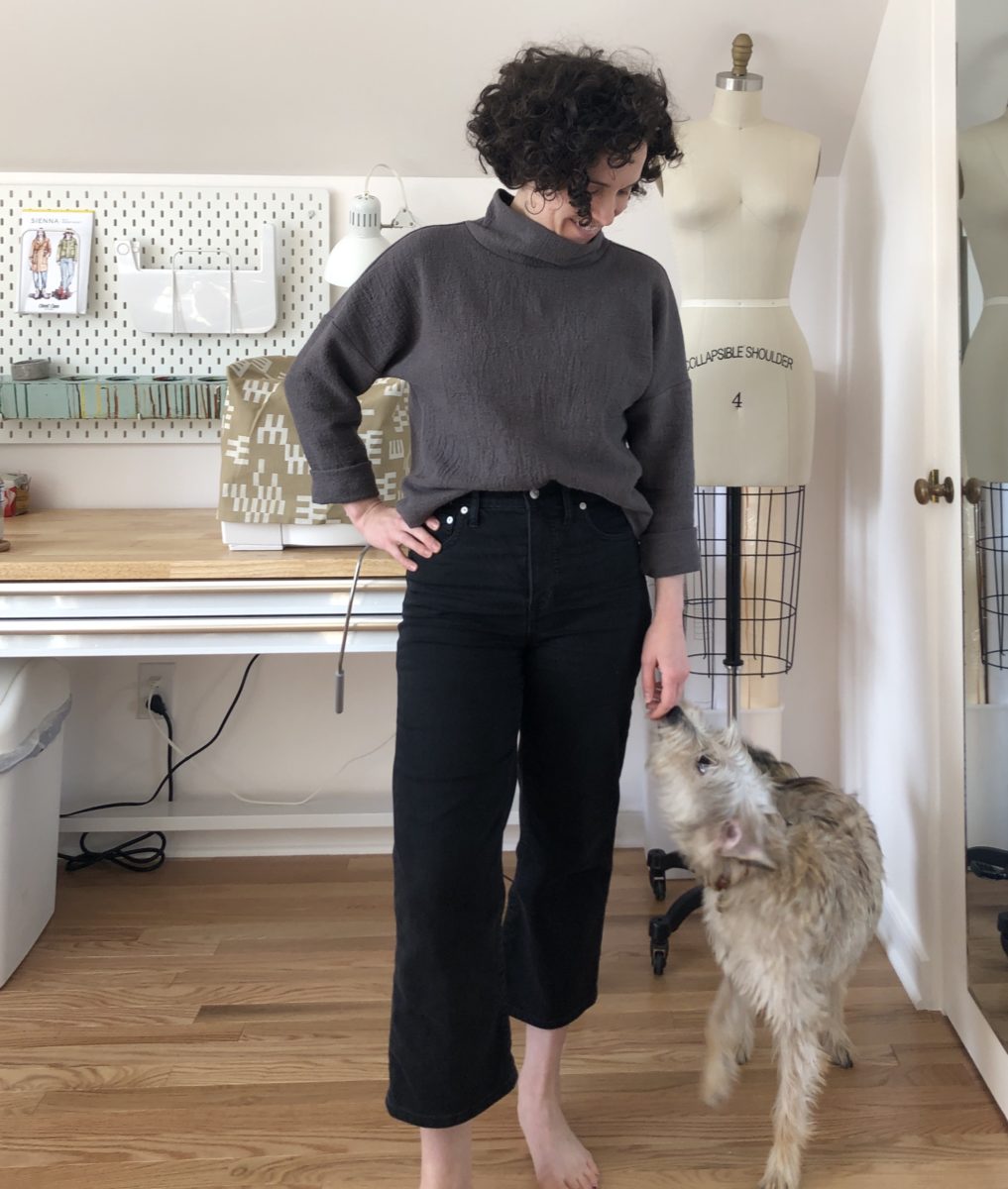
I’ve been in a making funk lately. Maybe it’s the weather, maybe it’s because work life isn’t killing my soul and I don’t need an outlet as much anymore. I don’t necessarily feel bad about it, it’s just weird to have idle hands.
I started writing this post well before COVID-19, but now I’m in even more of a personal making funk. I want to make things but my brain is really scattered and I’m finding the process not as satisfying.
I’m so grateful for my job, our house, food, the company of my husband and dog, and our current good health. I hope you have what you need during this weird and scary time and you are able to find some peace in making right now, or know it’s okay to take a break . Now on to the make details since I find looking at other’s makes a nice distraction.
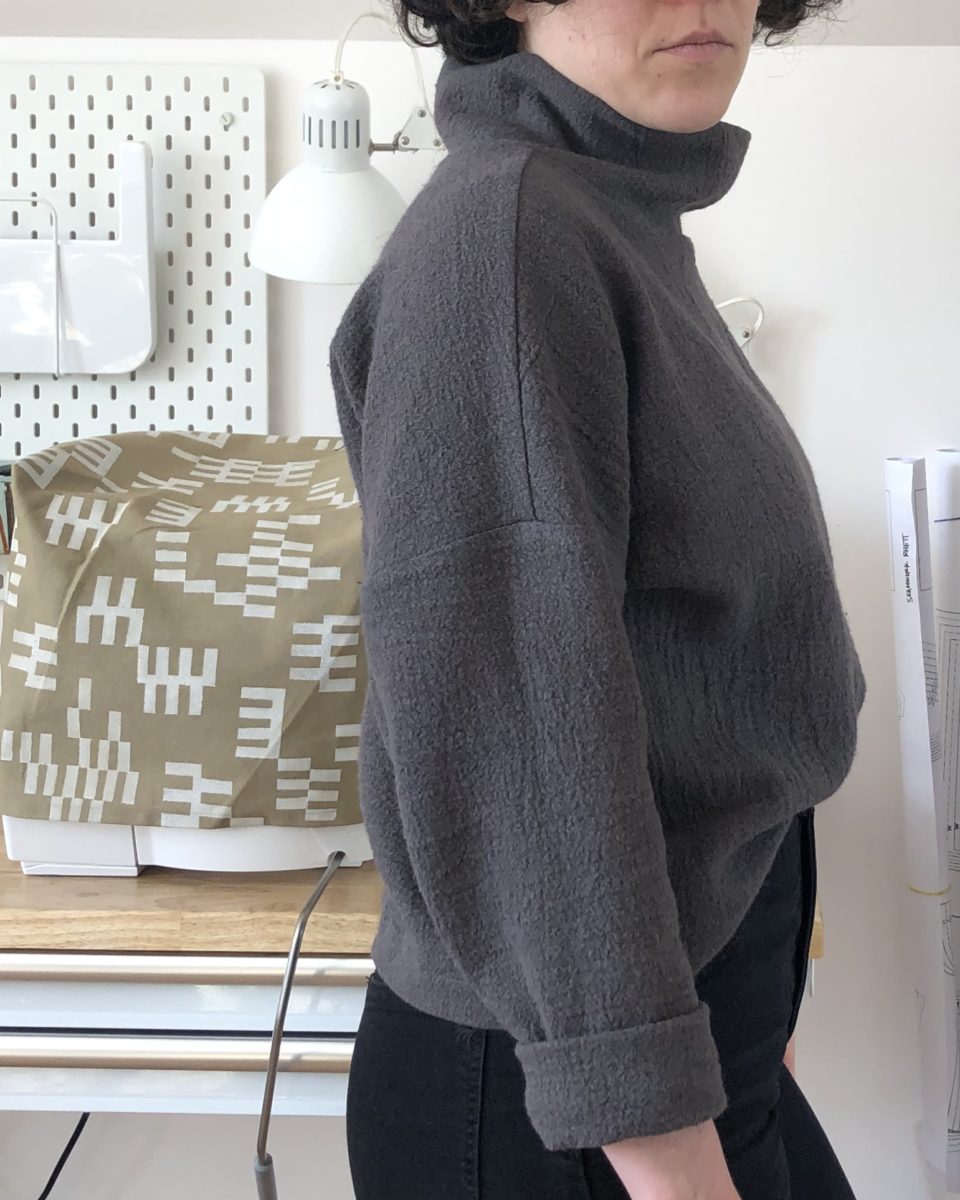
My first LB Pullover was made out of this super textural woven cotton I found at Bolt. I can’t find it on their website, but check them out anyway – they have a lot of amazing fabrics and if we’re able, we should support small fabric stores right now.
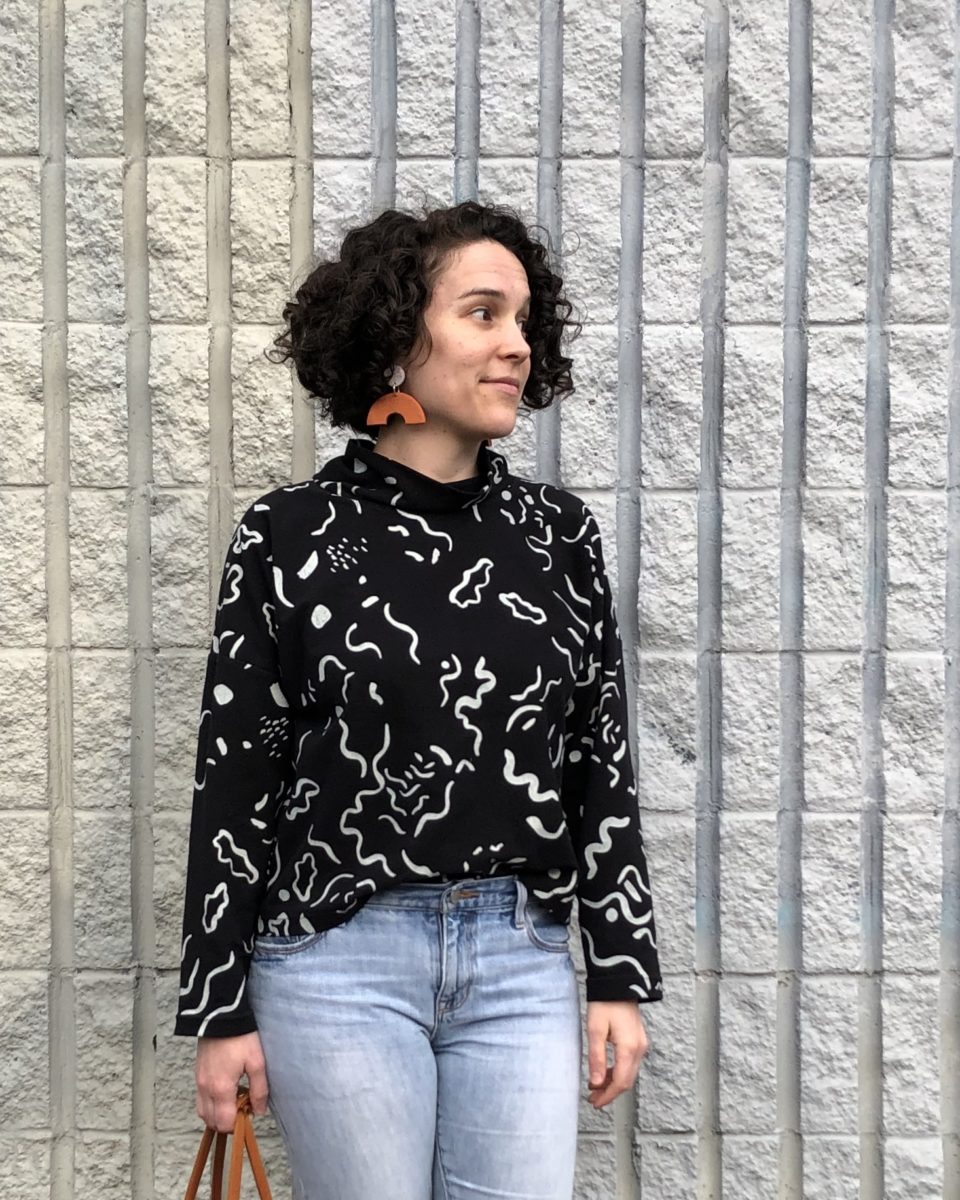
The second version I made used this drool-worthy jersey knit from North of West, another great small PDX business. The sister duo occasionally hosts warehouse sales where you can scoop up yards of fun fabric. I purchased three fabric bundles which had well over 12 yards of fabric! If you’re interested in scoring some of their fabric, follow them on Instagram and hopefully in the near future we can all meet up at their warehouse.
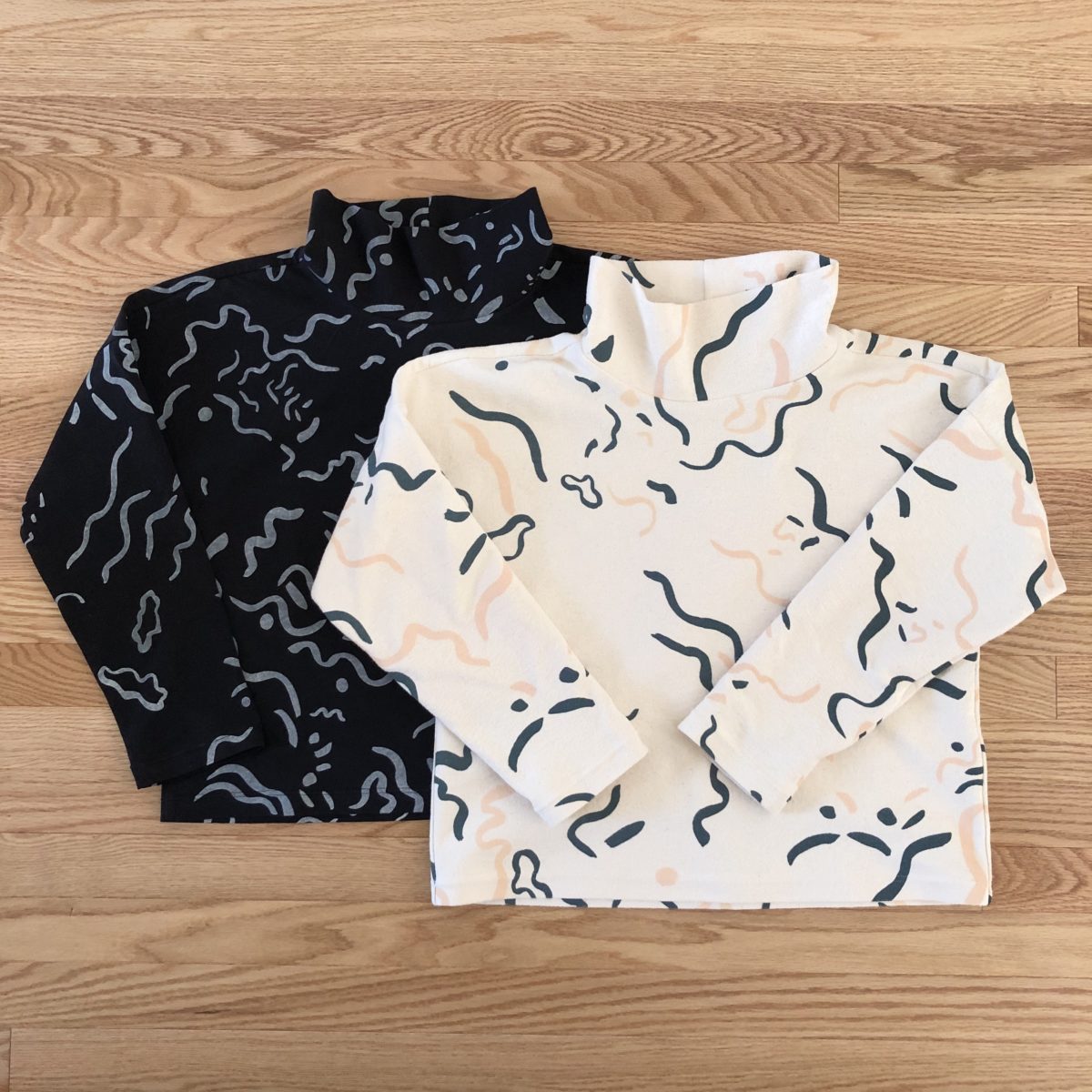
The third and fourth versions also used North of West fabric. The cream squiggle print is a yummy terry. The other black version I made for my mom.
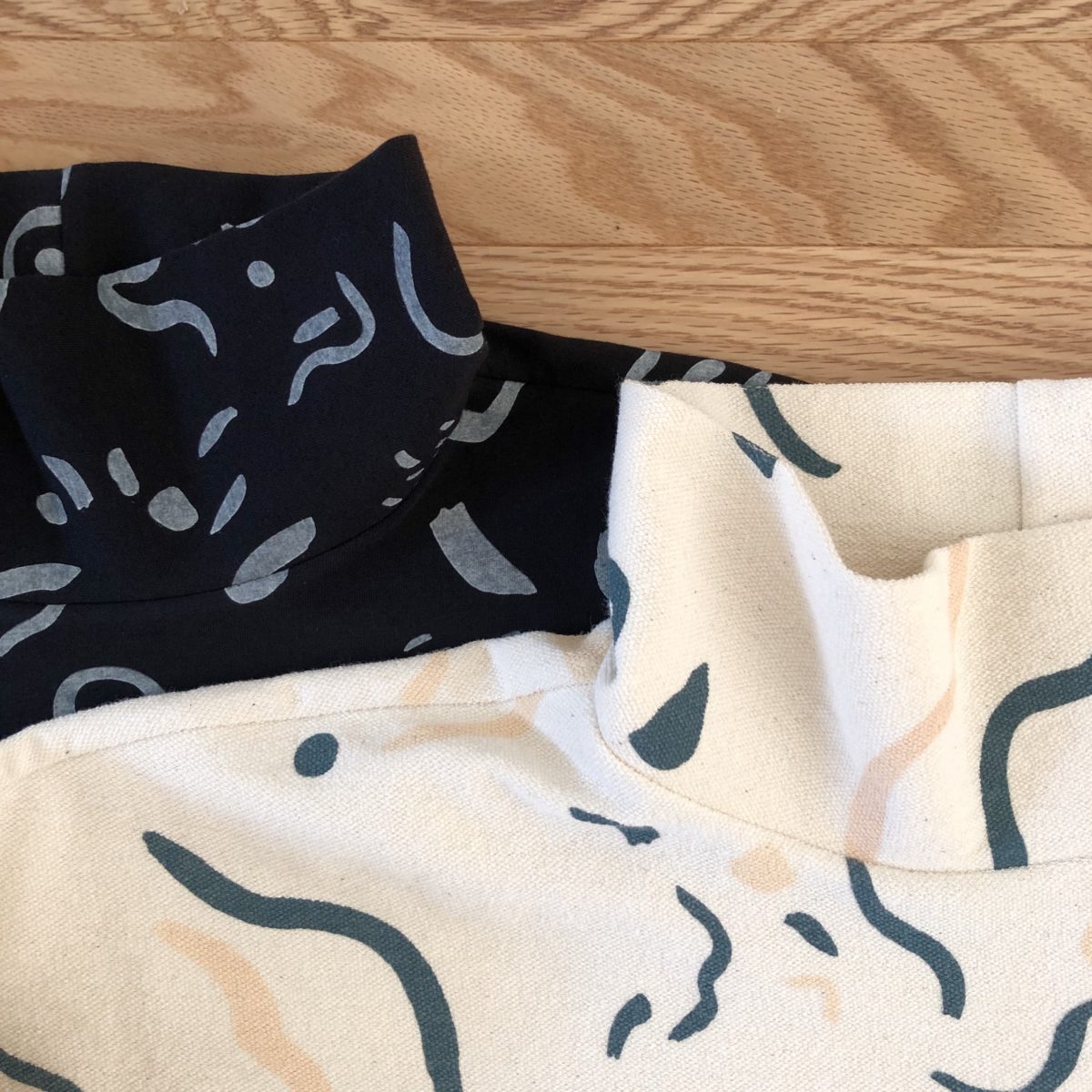
PATTERN – LB Pullover by Paper Theory
FABRICS – see above
SIZE – 8 for myself, 6 for my mom
MODS – none
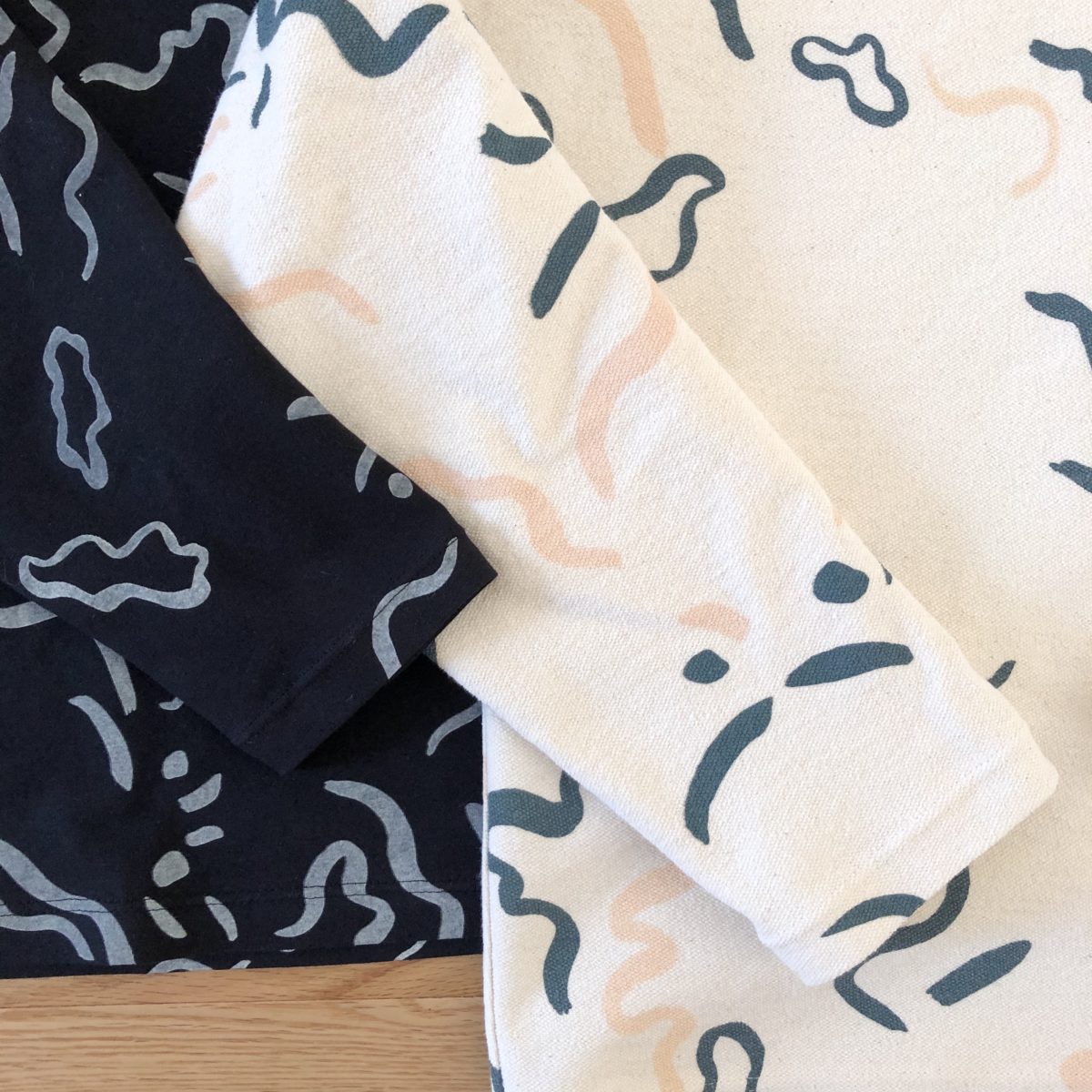
The LB Pullover is a great basic pattern – perfect for beginners, or if you’re wanting a quick and satisfying sew. I’m pretty much living in these right now.